Project A4 - ΔE-Effect Sensors
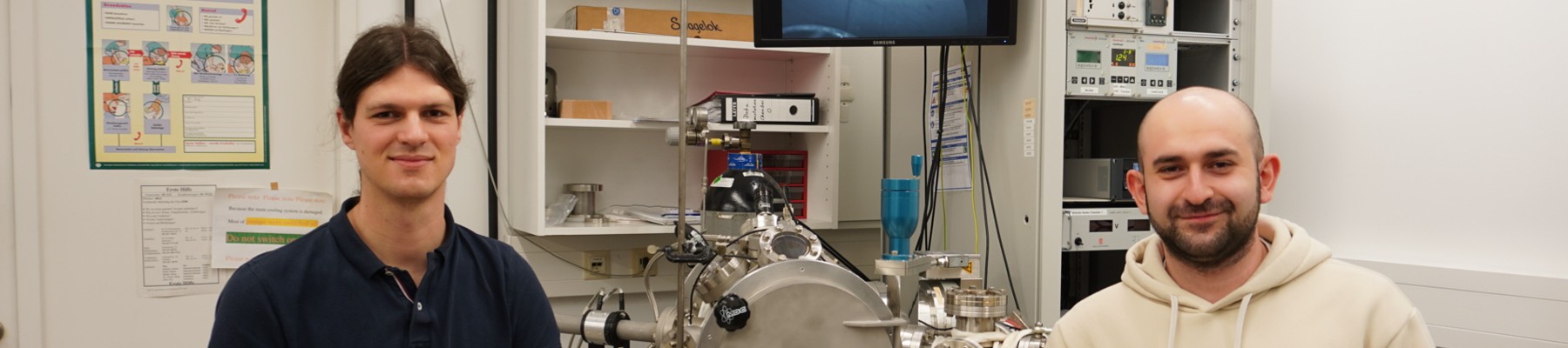
ΔE-effect magnetic field sensors utilize the resonance shift of a high frequency magneto-mechanical resonator in a magnetic field, due to the change in the stiffness of a magnetostrictive material, i.e., the ΔE effect. These sensors allow broadband magnetic field measurements at low frequencies down to DC with a very high dynamic range suitable for unshielded measurements. Moreover, they are robust against microphony effects and mechanical disturbances, which makes the sensor elements suitable for integration and miniaturization for compact sensor arrays.
This project focuses on the research of miniaturized ΔE-effect sensor matrices and their deployment in self-contained sensing cubes for planar and 3D magnetic field detection. Grounded in the theory and technology established in the previous funding period, we aim for spatially resolved multi-directional measurements with miniature sensor arrangements. Such matrices of magnetoelectric sensors with high spatial resolution or more than a few independent sensor elements currently do not exist. However, it is a crucial step towards versatile application of this technology. Addressing these shortcomings is especially important for applications targeting mobile measurements and magnetic field mapping. It will be investigated how robust sensing and processing nodes can be realized using MEMS (microelectromechanical systems) and integrated circuits including ASIC (application-specific integrated circuits) technology that enable a compact design of about 1 cm³ as a reliable sensing technology for biomedical applications. The specifications will be guided by initial target applications that allow us immediate proof of the concepts. The cubes with directional sensitivity are tailored to allow use in movement analysis and heart measurement as proposed in the projects B9 and B10 of this CRC.
Existing sensor system models will be extended to guide the system design with self-biased magnetic multilayers and enable scalable, three-dimensional sensor matrices, including flux concentrators and flux guides. Upon these findings, sensing structures will be devised and fabricated towards the medical applications pursued in the CRC and beyond. Each structure will include miniaturized electronics for edge-based signal processing, power management, and communication. This will be done using heterogeneous integration with components off the shelf, MEMS, and ASIC technology. In parallel, fundamental research on ΔE-effect sensors will be continued, with a focus on nonlinearities and the microscopic origin of carrier mediated magnetic noise, identified in the current funding period.
Involved Researchers
Person |
Role |
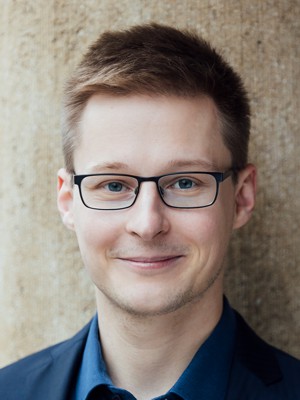 |
Dr.-Ing. Benjamin Spetzler Materials Science Energy Materials and Devices |
Project lead |
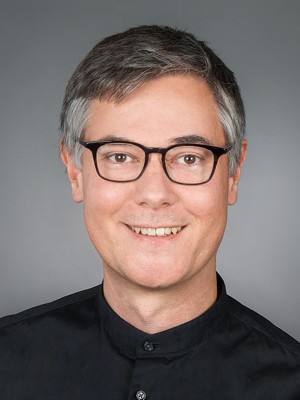 |
Prof. Dr. Robert Rieger Electrical Engineering Networked Electronic Systems |
Project lead |
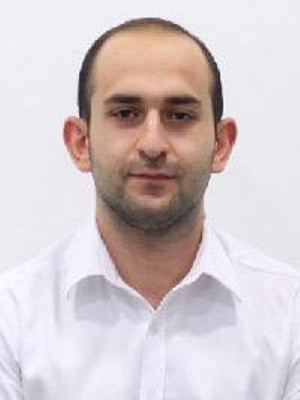 |
M.Sc. Fatih Ilgaz Materials Science Multicomponent Materials |
Doctoral researcher |
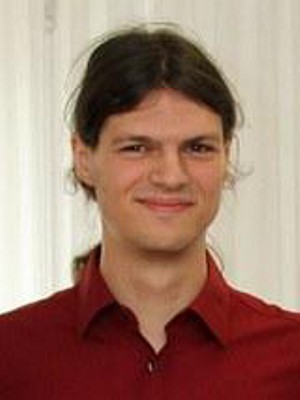 |
M.Sc. Patrick Wiegand Electrical Engineering Networked Electronic Systems |
Doctoral researcher |
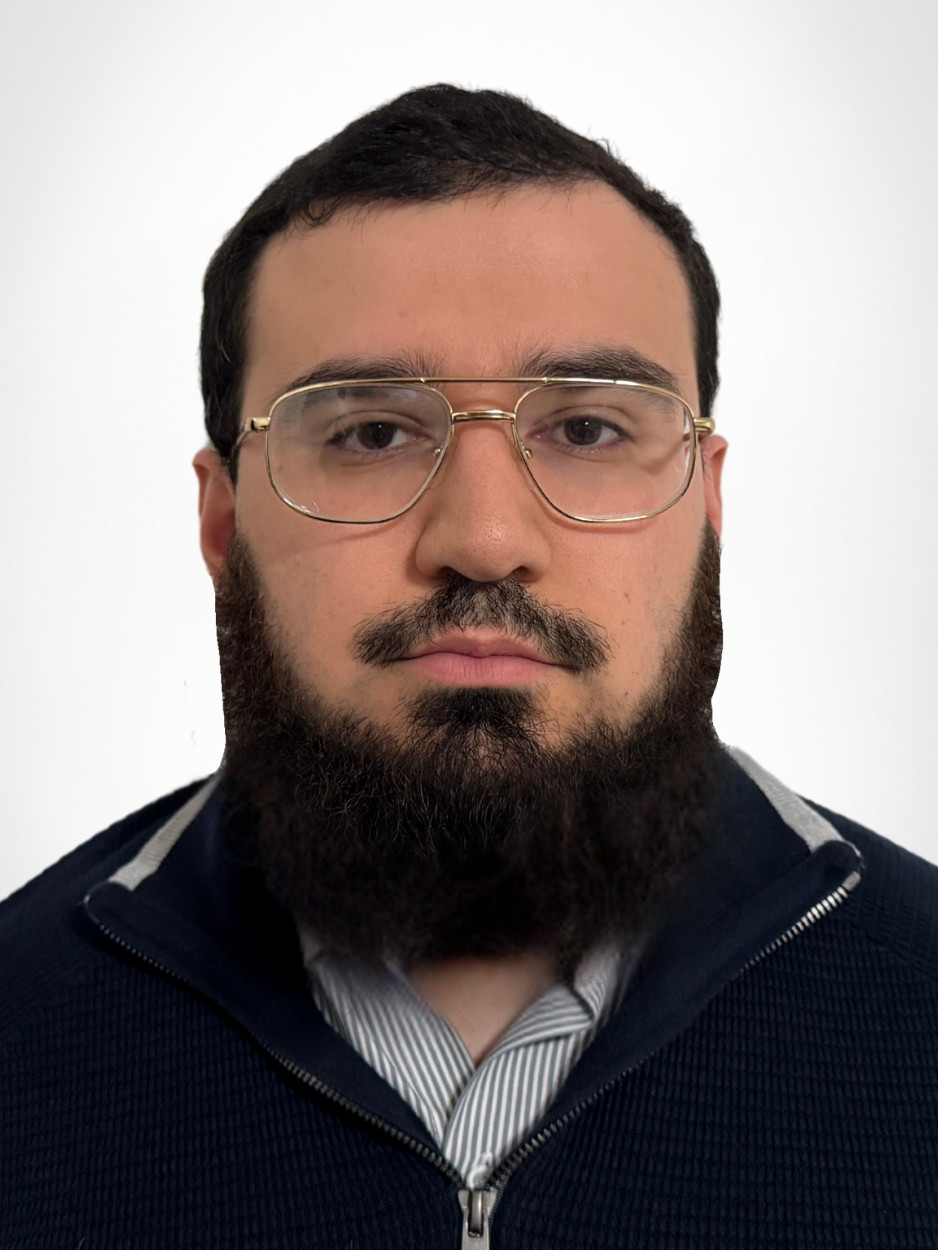 |
M.Sc. Ari A. Ahmad Materials Science Chair of Energy Materials and Devices |
Doctoral researcher |
Role within the Collaborative Research Centre
A close collaboration is envisioned with other projects in the CRC as summarized in the following table.
Furthermore, A4 is mainly involved in the following focus groups: F5 - Concepts based on Delta-E Effect,
F3 - Comparison of Sensor Concepts, F2 - Modelling and F1 - Magnetic Layers.
Collaborations |
A1 (Magnetostrictive Multilayers for Magnetoelectric
Sensors) |
Provides expertise on advanced magnetic multilayers and fluxgates. |
A6 (Microstructure and Structural Change of
Magnetoelectric Sensors) |
Improvement of process parameters in FeCoSiB deposition. |
A8 (Modelling of Magnetoelectric Sensors) |
Joint analysis of time-dependent behavior of ΔE-effect sensors. |
A10 (Magnetic Noise of Magnetoelectric Sensors) |
Magnetic characterization and modelling support of magnetic noise. |
B1 (Sensor Noise Performance and Analogue
System Design) |
Exchange on electronic circuit concepts for sensor readout. |
B2 (Digital Signal Processing), B9 (Magnetoelectric Sensors for Movement
Detection and Analysis), B10 (Magnetoelectric Sensor Systems for
Cardiologic Applications) |
Provision of sensor samples for research in the biomedical measurement and
signal processing applications. |
Z1 (MEMS Magnetoelectric Sensor Fabrication) |
Support with MEMS post processing, mainly deposition of magnetostrictive layer. |
Z2 (Magnetoelectric Sensor Characterization) |
Exchange of information and samples for improvement of sensor electronics. |
Project-related Publications
F. Ilgaz, E. Spetzler, P. Wiegand, F. Faupel, R. Rieger, J. McCord, B. Spetzler: Signal-noise Analysis of Miniaturized Delta-E Effect Magnetic Field Sensors, Applied Physics Letters, vol. 126, no. 8, 084103, 2025. |
P. Wiegand, S. Simmich, F. Ilgaz, F. Faupel, B. Spetzler, R. Rieger: ASIC Current-Reuse Amplifier with MEMS Delta-E Magnetic Field Sensors, IEEE Open Journal of Circuits and Systems, vol. 5, pp. 398-407, 2024. |
E. Spetzler, B. Spetzler, D. Seidler, J. Arbustini, L. Thormählen, E. Elzenheimer, M. Höft, A. Bahr, D. Meyners, J. McCord: On the Origin of Signal and Bandwidth of Converse Magnetoelectric Magnetic Field Sensors, Advanced Sensor Research, 4: 2400109, 2024. |
F. Ilgaz, E. Spetzler, P. Wiegand, F. Faupel, R. Rieger, J. McCord, B. Spetzler: Miniaturized Double-Wing ∆E-Effect Magnetic Field Sensors, Scientific Reports, vol. 14, no. 11075, 2024. |
E. Spetzler, B. Spetzler, J. McCord: A Magnetoelastic Twist on Magnetic Noise: The Connection with Intrinsic Nonlinearities, Advanced Functional Materials, no. 2309867, 2023. |
S. Simmich, P. Wiegand, R. Rieger: Noise Efficient Three-Channel Amplifier for MEMS Cantilever Readout, 19th Asia Pacific Conference on Circuits and Systems, conference proc., 2023. |
S. Simmich, R. Rieger: Analysis of Current-Reuse and Split-Voltage Topology for Biomedical Amplifier Arrays, IEEE PRIME, Villasimius, Italy, 2022. |
B. Spetzler, P. Wiegand, P. Durdaut, M. Höft, A. Bahr, R. Rieger, F. Faupel: Modeling and Parallel Operation of Exchange-Biased Delta-E Effect Magnetometers for Sensor Arrays, MDPI Sensors, vol. 21, no. 22, 759, 2021. |
S. Simmich, A. Bahr, R. Rieger: Noise Efficient Integrated Amplifier Designs for Biomedical Applications, MDPI Electronics, Special Issue: Analog Microelectronic Circuit Design and Applications, vol. 10, issue 13, 2021. |
B. Spetzler, C. Bald, P. Durdaut, J. Reermann, C. Kirchhof, A. Teplyuk, D. Meyners, E. Quandt, M. Höft, G. Schmidt, F. Faupel: Exchange Biased Delta-E Effect Enables the Detection of Low Frequency pT Magnetic Fields with Simultaneous Localization, Scientific Reports 11, Article no. 5269, 2021. |
B. Spetzler, E. V. Golubeva, R.-M. Friedrich, S. Zabel, C. Kirchhof, D. Meyners, J. McCord, F. Faupel: Magnetoelastic Coupling and Delta-E Effect in Magnetoelectric Torsion Mode Resonators, Sensors, vol. 21, no. 6, 2021. |
P. Durdaut, E. Rubiola, J.-M. Friedt, C. Müller, B. Spetzler, C. Kirchhof, D. Meyners, E. Quandt, F. Faupel, J. McCord, R. Knöchel, M. Höft: Fundamental Noise Limits and Sensitivity of Piezoelectrically Driven Magnetoelastic Cantilevers, Journal of Microelectromechanical Systems, vol. 29, issue 5, 2020. |
B. Spetzler, C. Kirchhof, J. Reermann, P. Durdaut, M. Höft, G. Schmidt, E. Quandt, F. Faupel: Influence of the Quality Factor on the Signal to Noise Ratio of Magnetoelectric Sensors Based on the Delta-E Effect, Applied Physics Letters, vol. 114, issue 18, 183504, 2019. |
J. Schmalz, B. Spetzler, F. Faupel, M. Gerken: Love Wave Magnetic Field Sensor Modeling — from 1D to 3D Model, International Conference on Electromagnetics in Advanced Applications (ICEAA), pp. 0765-0769, 2019. |
A. Kittmann, P. Durdaut, S. Zabel, J. Reermann, J. Schmalz, B. Spetzler, D. Meyners, N. X. Sun, J. McCord, M. Gerken, G. Schmidt, M. Höft, R. Knöchel, F. Faupel, E. Quandt: Wide Band Low Noise Love Wave Magnetic Field Sensor System, Scientific Reports, vol. 8, no. 278, 2018. |
P. Durdaut, J. Reermann, S. Zabel, C. Kirchhof, E. Quandt, F. Faupel, G. Schmidt, R. Knöchel, M. Höft: Modeling and Analysis of Noise Sources for Thin-Film Magnetoelectric Sensors Based on the Delta-E Effect, IEEE Transactions on Instrumentation and Measurement, vol. 66, no. 10, pp. 2771-2779, 2017. |
S. Zabel, J. Reermann, S. Fichtner, C. Kirchhof, E. Quandt, B. Wagner, G. Schmidt, F. Faupel: Multimode Delta-E Effect Magnetic Field Sensors with Adapted Electrodes, Applied Physics Letters, 108, 222401, 2016.
|