Project A2 - Hybrid Magnetoelectric Sensors Based on Mechanically Soft Composite Materials
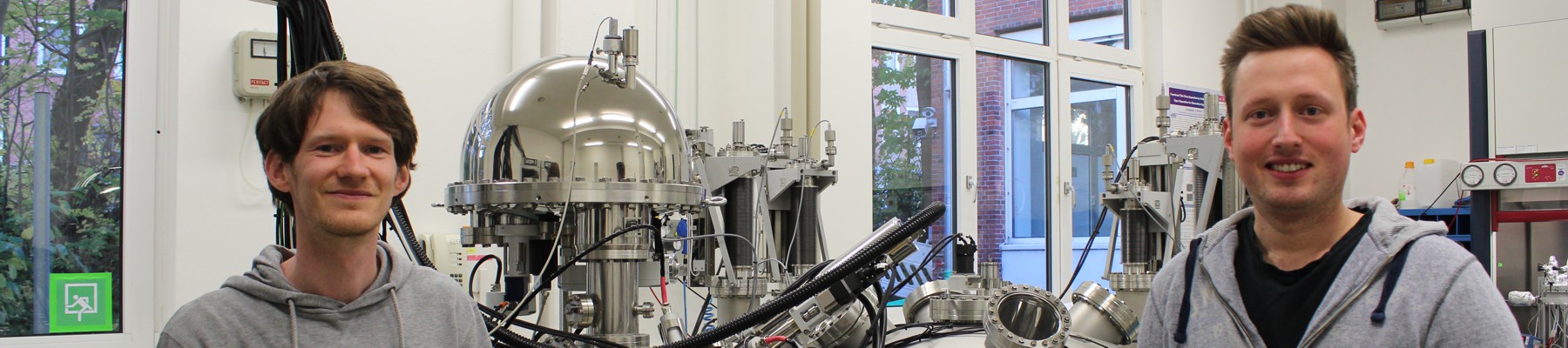
Project A2 is concerned with the development of wearable magnetoelectric sensor systems based on mechanically soft composite materials, the principles of which are being utilized and further researched for biomedical applications. Composite variants include as well the most elementray magnetic composite. This is based on at least two permanent magnets interacting with the magnetic field of interest as the only two “particles” of the composite connected by a mechanically soft structure. The mechanically soft composite containing magnetic microparticles is termed microcomposites, while the latter with macroscopic magnets is referred to as macrocomposite. The project builds upon successful micro- and macrocomposite sensor designs from the current funding period, including flexible sensor structures, integrated energy harvesting, as well as flexible electret thin films as pseudo piezoelectric materials. Beyond corona discharged electrets a new electret class, where no charging step is necessary to create excess charges, was developed. Spontaneous polarization, proportional to the thickness of the electret, guarantees a permanent electrical surface potential as electrical analog to a permanent magnet.
With the newest findings, sensors with permanent (hard) magnetic particles or permanent magnets will be combined with permanent electrets. This ensures that absolutely no intrinsic electric and magnetic noise sources are present in the sensor materials within the measurement range of the applications and an insensitivity to DC fields. Measurements with the sensors do not require a magnetic bias field and can be performed unshielded in the presence of the earth’s magnetic field. These sensors are implemented in a flexible, organic, printed ME-sensor and electronics setup, making them compatible with various applications which require wearability of the sensors. Thus, this research project is in close cooperation with projects from the B area: It will support B9 for the movement analysis through adaptive sensor devices that allow e.g., a tuning of the resonance frequency depending on the requirements of the application. Furthermore, the project will develop wearable patches (in collaboration with project B10), with all electronics integrated, which does not interfere with magnetic diagnostics like MCG for example. The additive manufacturing method of inkjet printing will be employed to precisely print carbon paste, serving as electrodes and conductive pathways in mentioned flexible and wearable applications. More complex structures can be realized with other additive manufacturing techniques such as 3D printing, which can be also integrated with the flexible materials. Custom made printers are available which go beyond filament and lithography 3D printing, enabling the printing of silicone for instance. Close collaboration with the simulation (A10) and microstructural characterization (A6) ensures a comprehensive understanding of the micro and macrocomposite system in theory and microstructure.
Involved Researchers
Person |
Role |
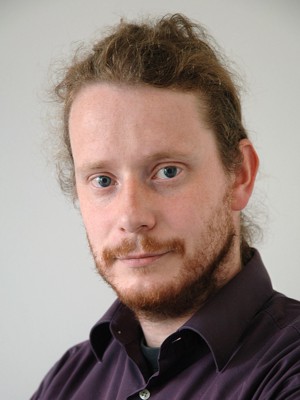 |
Prof. Dr. Rainer Adelung Materials Science Functional Nanomaterials |
Project lead |
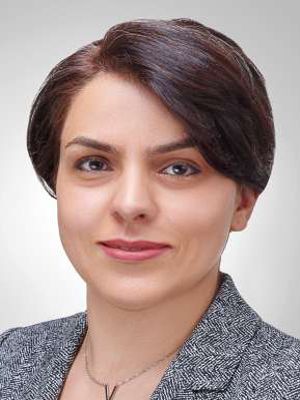 |
Prof. Dr. Tayebeh Ameri Materials Science Composite Materials |
Project lead |
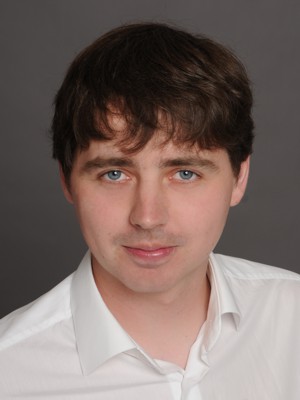 |
Dr. Sören Kaps Materials Science Functional Nanomaterials |
Project lead |
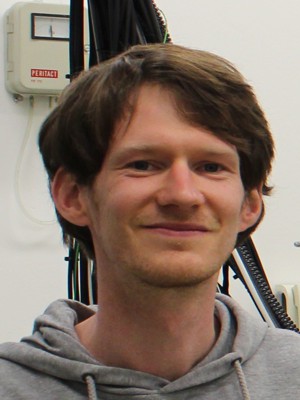 |
Dr.-Ing. Stefan Schröder Materials Science Multicomponent Materials |
Doctoral researcher |
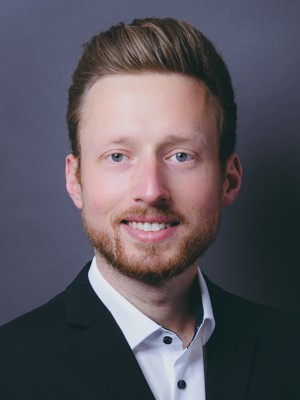 |
M.Sc. Lukas Zimoch Materials Science Functional Nanomaterials |
Doctoral researcher |
Role within the Collaborative Research Centre
Project A2 is involved in the focus groups F3 - Comparison of Sensor Concepts and F6 - Biomedical Applications. As mentioned in the above work plan, cooperations with the following projects are targeted:
Collaborations |
A6 (Microstructure and Structural Change of
Magnetoelectric Sensors) |
Microstructural characterization. |
A10 (Magnetic Noise of Magnetoelectric Sensors) |
Simulation of composites. |
B9 (Magnetoelectric Sensors for Movement
Detection and Analysis) |
Support for the movement analysis. |
B10 (Magnetoelectric Sensor Systems for
Cardiologic Applications) |
Exchange on implantable devices, develop an ECG patch. |
Z1 (MEMS Magnetoelectric Sensor Fabrication) |
Powder magnets, Z1 provides cantilevers used in WP1 |
Z2 (Magnetoelectric Sensor Characterization) |
Magnetic characterization. |
Project-related Publications
L. Zimoch, S. Schröder, E. Elzenheimer, S. Kaps, T. Strunskus, F. Faupel, M. Höft, R. Adelung: Electret Integrated Magnetic Field Sensor Based on Magnetostrictive Polymer Composite with nT Resolution, Scientific Reports, vol. 15, 1561, 2025. |
M. Gerhardt, L. Zimoch, C. Dorn, E. Elzenheimer, C. Bald, T. Lerg, J. Hoffmann, S. Kaps, M. Höft, G. Schmidt, S. Wulfinghoff, R. Adelung: Self-powered Elementary Hybrid Magnetoelectric Sensor, Nano Energy, vol. 115, 108720, 2023. |
S. Schröder, N. Ababii, O. Lupan, J. Drewes, N. Magariu, H. Krüger, T. Strunskus, R. Adelung, S. Hansen, F. Faupel: Sensing Performance of CuO/Cu2O/ZnO: Fe Heterostructure Coated with Thermally Stable Ultrathin Hydrophobic PV3D3 Polymer Layer for Battery Application, Materials Today Chemistry, vol. 23, pp. 100642, 2021. |
A. Komijani, S. Schröder, T. Strunskus, F. Faupel: Multi-pin Corona Poling Rotating System for ME Electret Sensors, 18th IEEE International Symposium on Electrets (ISE 18), Shanghai, China, 24-28 September, 2021. |
S. Schröder, A. M. Hinz, T. Strunskus, F. Faupel: Molecular Insight into Real-Time Reaction Kinetics of Free Radical Polymerization from the Vapor Phase by In-Situ Mass Spectrometry, J. Phys. Chem. A., 125, pp. 1661−1667, 2021. |
M. H. Burk, D. Langbehn, G. Hernández Rodríguez, W. Reichstein, J. Drewes, S. Schröder, S. Rehders, T. Strunskus, R. Herges, F. Faupel: Synthesis and Investigation of a Photoswitchable Copolymer Deposited via Initiated Chemical Vapor Deposition for Application in Organic Smart Surfaces, ACS Appl. Polym. Mater., 3, 3, 1445–1456, 2021. |
S. Schröder, O. Polonskyi, T. Strunskus, F. Faupel: Nanoscale Gradient Copolymer Films Via Single-Step Deposition from the Vapor Phase, Materials Today, vol. 37, pp. 35-42, 2020. |
M. H. Burk, S. Schröder, W. Moormann, D. Langbehn, T. Strunskus, S. Rehders, R. Herges, F. Faupel: Fabrication of Diazocine-Based Photochromic Organic Thin Films via Initiated Chemical Vapor Deposition, Macromolecules, vol. 53, issue 4, pp. 1164–1170, 2020. |
M. Scharnberg, S. Rehders, Ö. Adiyaman, S. Schröder, T. Strunskus and F. Faupel: Evaporated Electret Films with Superior Charge Stability Based on Teflon AF 2400, Organic Electronics, vol. 70, pp. 167-171, 2019. |
S. Schröder, T. Strunskus, S. Rehders, K. K. Gleason, F. Faupel: Tunable Polytetrafluoroethylene Electret Films with Extraordinary Charge Stability Synthesized by Initiated Chemical Vapor Deposition for Organic Electronics Applications, Scientific Reports, 9, no. 2237, 2019. |
M. Mintken, M. Schweichel, S. Schröder, S. Kaps, J. Carstensen, Y. K. Mishra, T. Strunskus, F. Faupel, R. Adelung: Nanogenerator and Piezotronic Inspired Concepts for Energy Efficient Magnetic Field Sensors, Nano Energy, vol. 56, pp. 420-425, 2019. |
O. C. Aktas, S. Schröder, S. Veziroglu, M. Z. Ghori, A. Haidar, O. Polonskyi, T. Strunskus, K. K. Gleason, F. Faupel: Superhydrophobic 3D Porous PTFE/TiO2 Hybrid Structures, Advanced Materials Interfaces, vol. 6, 1801967, 2019. |